РУЧНАЯ ДУГОВАЯ СВАРКА ПЛАВЯЩИМСЯ ЭЛЕКТРОДОМ
Техника Сварки. При зажигании дуги напряжение между электродом и свариваемым изделием обычно равно 60 В, для электродов отдельных промышленных марок напряжение холостого хода должно быть повышено до 70 В. При замыкании сварочной цепи напряжение падает почти до нуля и после возбуждения дуги поддерживается в пределах 16—30 В в зависимости от длины дуги и марки электрода.
Основными характеристиками процесса плавления электрода является количество расплавленного электродного металла в, и относительные потери (коэффициент потерь) электродного металла в процессе сварки из›за разбрызгивания, испарения и окисления.
При установившемся процессе сварки плавление электрода под действием дуги происходит равномерно по следующей приближенной зависимости, установленной опытным путем при большой плотности тока. Коэффициент расплавления зависит от материала электродного стержня и состава обмазки, покрывающей его поверхность, от рода и полярности тока и колеблется в пределах 8—14 г/А-ч. При сварке на постоянном токе он несколько повышается.

Потери наплавленного металла, определенные разностью массы расплавленного металла электрода и массы металла, образующего шов, определяются коэффициентом. Величина возрастающая с увеличением тока, меняется в пределах 5—30% для обычных электродов. Коэффициент также зависит от стабильности процесса сварки и особенностей отрыва и переноса капель через дуговой промежуток. Коэффициент расплавления изменяется незначительно с повышением плотности тока. В процессе сварки электродами на токе большей плотности скорость плавления увеличивается за счет подогрева стержня током.
Сварку швов в вертикальном и потолочном положениях выполняют, как правило, электродами диаметром 4 мм. При этом сила тока должна быть на 10-20% ниже, чем для сварки в нижнем положении.
Для получения валика постоянной ширины необходимо, чтобы в процессе сварки поперечные колебания электрода и скорость его перемещения вдоль шва не менялись, при этом амплитуда поперечных колебаний не должна превышать
Увеличение диаметра электрода ограничено возможностью возникновения прожогов свариваемого изделия, затруднением сварки швов в вертикальном и потолочном положениях, а также возникновением непровара при наложении первого слоя, который в многослойном шве обычно выполняют электродами диаметром 4—5 мм. При укладке первого слоя многослойного шва электрод ведут без поперечных колебаний.
Дефекты сварных соединений.
Непровар - дефект в виде местного несплавления в сварном соединении вследствие неполного расплавления кромок или поверхностей ранее выполненных валиков. На рисунке показаны примеры непровара по кромке (а) и по сечению (б‚ в). Причинами непровара могут быть неправильное ведение процесса сварки, загрязнение поверхности металла. недостаточный ток и др.
Подрез зоны сплавления - дефект в виде углубления на основном металле вдоль линии сплавления сварного шва с основным металлом. На рисунке в показаны подрезы в зоне сплавления в стыковых и угловых швах.
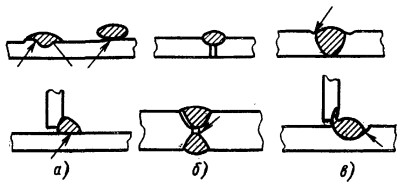
Трещина сварного соединения - дефект в виде разрыва в сварном шве и прилегающих к нему зонах. Различают трещины сварного соединения продольные (ориентированные параллельно продольной оси сварного шва); поперечные (ориентированные перпендикулярно продольной оси cварного шва); разветвленные (имеющие ответвления в различных направлениях); микротрещины (обнаруживаемые при увеличении не менее 50x); сетку трещин.
Трещины являются наиболее опасными видами дефектов сварных соединений, которые могут привести к разрушению конструкций при нормальных или пониженных нагрузках.
Склонность сварных швов к образованию трещин зависит от химического состава металла шва, жесткости конструкций. режима сварки, последовательности наложения швов и т. п.
Поры сварного шва - дефект в виде полости округлой формы, заполненной газом. Поры могут быть поверхностными, внутренними или располагаться в линию (цепочка пор сварного шва). Поры в сварном шве обычно имеют сферическую форму. Газовые пузыри образуются в результате перенасыщения жидкого металла газами, которые не успевают выйти на поверхность шва во время его кристаллизации.
Неметаллические включения сварного шва - дефект в виде неметаллической частицы в металле шва. Неметаллические включения в сварном шве - макро- и микроскопические частицы соединений металла с кислородом (оксиды), азотом (нитриды), серой (сульфиды,) фосфором (фосфиды). Различают эндогенные включения, т. е. такие включения, которые образуются в результате протекания в металле процессов (например, химических реакций), и экзогенные включения в результате попадания инородных частиц. В сварном шве могут иметь место включения: шлаковые, окисные и металлические (дефект в виде частиц инородного металла в металле шва).
К дефектам сварных швов также относятся брызги металла (дефект в виде затвердевших капель металла на поверхности сварного соединения), поверхностное окисление сварного соединения (дефект в виде окалины. пленки окислов или цветов побежалости), наплав на сварном соединении (дефект в виде натекания металла шва на поверхность основного металла или ранее вынолиенного валика без сплавления с ним). превышение усиления, занижение размеров сечения и неплавное сопряжение сварного шва. превышение проплава, смещение сварных кромок.
Основные типы сварных соединений. К основным типам сварных соединений относятся стыковые, тавровые, угловые, внахлестку и прорезные. Тип шва определяется формой поперечного сечения подготовки кромок свариваемых изделий.
Форма поперечного сечения подготовленных кромок и выполненного шва установлена ГОСТ 5264 - 69 и 11534 - 75. Форма разделки кромок определяется толщиной сварИваемого металла и положением шва в пространстве.
Скошенные кромки притупляют, чтобы предотвратить сквозное проплавление (прожоги) корня шва. Для лучшего провара между свариваемыми кромками оставляют зазор. Форма разделки кромок должна обеспечить возможность свободного манипулирования электродом при сварке при возможно меньшем объеме шва. Зазоры и размеры разделки кромок должны быть неизменными по всей длине соединения в пределах допусков.
При больших толщинах, начиная с 12 мм, применяются двусторонние скосы кромок или криволинейные скосы одной или двух кромок. Преимущество двустороннего или криволинейного скоса кромок заключается в меньшем по сравнению с односторонним скосом объеме наплавленного металла, расходе сварных электродов; снижении деформаций, сопутствующих сварке.
Соединения внахлестку, втавр и прорезные выполняют угловыми (валиковыми) швами. Соединения внахлестку можно выполнять электрозаклепками.
Различают также швы непрерывные (сплошные) и прерывистые. Прерывистыми швами и электрозаклепками сваривают соединения, не требующие герметичности. Швы бывают усиленными (выпуклыми), без усиления и ослабления (вогнутые).
Подготовку кромок под сварку можно производить газовыми резаками (вручную, полуавтоматом, автоматом), на кромкострогальном станке, на токарном станке, пневматическими зубилами. После газовой резки кромки не должны иметь надрезов, выплавленных углублений и зазубрин.
При сварке встык листов неоднородной толщины наибольшую. предельную разность толщин выбирают в зависимости от толщины тонкого листа, руководствуясь ГОСТ 5264—69. Подготовку кромок под сварку производят так же, как для листов одинаковой толщины, конструктивные элементы подготовленных кромок и размеры выполненного шва сварного соединения выбирают по большей толщине 51, руководствуясь примечанием к табл. 1 ГОСТ 5264—69. Усиление шва допускается не более 2 мм для швов, выполненных в нижнем положении, и не более 3 мм для швов, выполненных во всех пространственных положениях.
Ослабление шва сварного соединения (А) при сварке во всех пространственных положениях допускается не более 3 мм. При двусторонней сварке допускается удалять ранее наложенный корень шва до чистого металла любым способом. Допускается увеличение предельных отклонений усиления шва, выполняемого в вертикальном, горизонтальном и потолочном положениях.
Форма подготовки кромок, размеры поперечного сечения шва регламентированы ГОСТ 5264—69. В нем предусмотрены 25 видов стыковых соединений, 10 угловых, 11 тавровых и три вида соединений внахлестку; соответственно им присвоены обозначения С, У, Т и Н. Всем видам соединений присвоены порядковые номера, ГОСТ 11534—75 регламентирует восемь угловых и восемь тавровых соединений.
Особенности выполнения сварных швов различных типов. Влияние магнитных полей на сварочную дугу. Столб сварочной дуги можно рассматривать как гибкий проводник, по которому проходит электрический ток. Собственное магнитное поле дуги и поле сварочного контура (ферромагнитных масс) вызывает явление, известное под названием «магнитного дутья».
Магнитное дутье может затруднять сварку дугой постоянного тока, особенно при повышении его значения, так как сила воздействия магнитного поля приблизительно пропорциональна квадрату тока. Продольное магнитное поле улучшает технологические свойства дуги; под действием поперечного магнитного поля сварочная дуга отклоняется.
Результирующий магнитный поток, равный геометрической сумме магнитных потоков сварочного и вихревых токов, значительно меньше магнитного потока при постоянном токе; кроме того, он сдвинут по фазе относительно сварочного тока, что ослабляет электромагнитную силу взаимодействия магнитного поля с током.
Для ослабления нежелательного действия магнитного дутья при сварке рекомендуется применять следующие меры: наклонять электрод; изменять место подключения сварочного провода к изделию; применять переменный ток и т. п.
Влияние размеров сварочной ванны на процесс сварки. Способность ванны деформироватъся называется текучестью ванны, которая зависит от запаса теплоты (энтальпии), условий охлаждения вытекающего металла и размеров ванны, так как энтальпия металла в разных зонах ее неодинакова. Наиболее нагретым (а потому наиболее подвижным) является металл головной части ванны, в хвостовой же ее части температура металла снижается и вязкость его нарастает. Вблизи стенок ванны, даже в головной ее части, имеется слой металла, находящийся в твердо-жидком состоянии. Чем больше размер ванны, тем больше ее текучесть. Текучесть сварочной ванны является важным фактором, определяющим формирование шва.
Сопоставляя электроды различных марок по массе ванны при одном и том же режиме сварки, можно подразделить их на три группы:с малым значением (например, БЛАГА-25), со средним значением (например, УОНИ-13) и электроды с большим значением (например, ОЗС-З). Такое подразделение электродов соответствует их разбивке по технологическим свойствам: электроды с наименьшей массой ванны, электроды промежуточного типа и электроды с наибольшей массой ванны. Электроды с наименьшей массой ванны (их иногда называют «холодными» электродами) позволяют вести сварку в любом пространственном положении; электроды промежуточного типа позволяют вести сварку во всех пространственных положениях. Электроды с наибольшей массой ванны (их иногда называют «горячими» электродами), не пригодны для сварки в потолочном, вертикальном и наклонном положениях. Таким образом, масса ванны является основным показателем, характеризующим возможность применения сварки в том или ином пространственном положении. В пределах одного процесса масса ванны может значительно изменяться за счет режима сварки.
Изменение массы ванны при одном и том же режиме сварки (при одной силе тока и скорости сварки) для различных типов электродов объясняется разными коэффициентами расплавления ее и напряжением дуги. Массу, которая является предельно допустимой, обеспечивающую сварку в данных технологических условиях, например в потолочном положении называют критической массой. Установлено, что критическая масса ванны зависит от ее положения в пространстве, от толщины свариваемого металла и глубины проплавления. Режим сварки надо выбирать исходя из того чтобы при всех условиях (в данном пространственном положении) масса ванны была меньше критической.
Нагрев и охлаждение металла ванны и отчасти свариваемого металла можно просто и достаточно эффективно регулировать с помощью колебательного движения электрода. Колебания электрода (поперечные. продольные или комбинированные) позволяют в известных пределах рассредоточить тепловон поток в ванне, охлаждая металл при отводе электрода с того или иного участка ванны и тем самым устраняя течение металла в нежелательном направлении. Колебательные движения электрода уменьшают опасность появления прожогов, возможность стекания металла при наклонном положении сварочной ванны, а также выпуклость шва со стороны дуги, что облегчает сварку последующих слоев.